“The robot in bay 5 is broken”: 4 ways you can use facility insights to drive performance and control costs
Convoy News, Shippers • Published on June 7, 2022
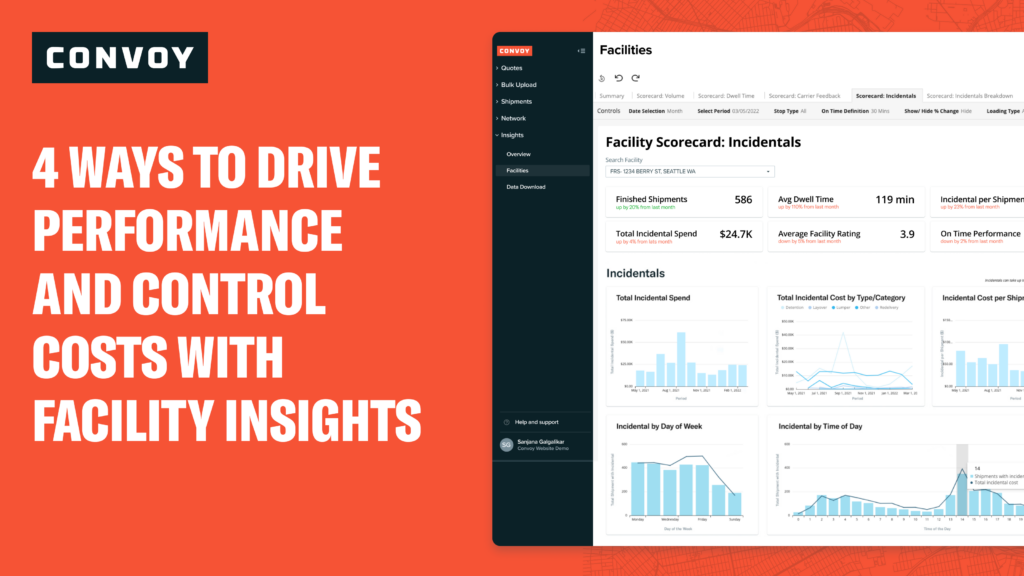
Why have our incidental costs increased so much? What is going on with the dwell times in San Antonio? It can take shippers months to get to the root cause of problems like these. Without detailed visibility into what’s happening at the facility level, shippers don’t know what they can’t see.
But what if feedback was available across your entire network? What if you could see not only what was happening but also what you could do about it? What if your freight provider came to you and said, “Hey, we noticed a spike in incidentals at one of your facilities, and driver feedback indicates this is because of a broken robot on bay 5. It has cost you $18k in incremental spend in the last 30 days. How much would it cost for you to fix it?”
For this beverage manufacturer with the broken robot, the facility wasn’t reporting the issue to management, and they didn’t know what they couldn’t see — until we surfaced it. Convoy leverages robust data sets from our tech-connected carrier network of more than 400,000 trucks, boosted by an analytics and visualization platform that turns this data into real-time insights.
Starting today, Convoy shippers can get on-demand access to facility insights to help:
- Identify trends that help save costs. Track your incidental spend per shipment for each facility and break out incidentals by type, day of the week, or even time of day.
- Drive operational performance. Get granular visibility into each facility’s average dwell time and on-time performance, including filters to quickly see the lowest-performing facilities in your network.
- Get timely carrier feedback. See carrier retention, verbatim reviews, and star ratings for each facility.
Watch this video to hear Abhi Krishnappa, one of Convoy’s engineering managers, tell you more about what’s new.
So how exactly can facility insights help drive performance and control costs? Here are a few real-world examples.
1. Why did my incidental spend jump month over month at my highest volume facility?
The problem: A shipper noticed an unexpected 23% month-over-month increase in incidentals per shipment at their highest trafficked facility.
The process: They looked at the facility’s scorecards and discovered dwell time nearly doubled when volume increased by almost 20% within the same time frame.
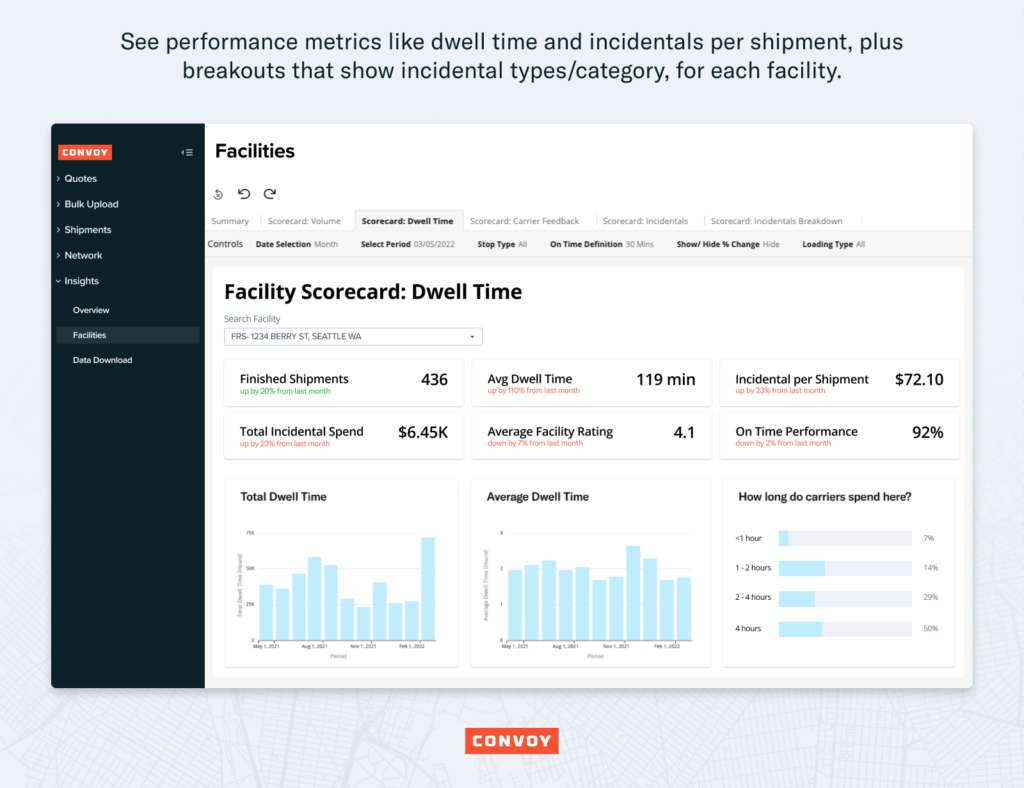
The insight: The volume was taxing the facility’s ability to get trucks in and out, increasing dwell times for carriers and therefore detention costs — the number one incidental contributor — to the shipper. The shipper, in partnership with their Convoy account team, decided on a solution: a combination of load balancing and rerouting shipments to other facilities.
TIP: Dwell time is the single most important determinant of facility rating, according to Convoy’s Annual Freight Insights Report. Long wait times frustrate carriers, who make a living moving freight, and can end with bad reviews like “had to wait 3 hours for what was supposed to be a preloaded trailer. Never picking a load from here again.” According to Convoy research, negative facility ratings can increase the rate per mile from 5% to as much as 20%.
2. How can I reduce detention costs at this problematic facility?
The problem: A shipper struggled with bottlenecks and backups at their loading docks, but anecdotally, they couldn’t point to any specific problems or patterns.
The process: Data within the incidentals scorecard of their dashboard showed detention started to increase at 1 p.m., reached its max point between 2 p.m. and 3 p.m., but returned to normal by 6 p.m. With these times of day, the shipper and Convoy together looked at shipment volume and detention costs, uncovering that they were paying an extra $40 per load, on more loads, during their peak hours from 2 p.m. and 3 p.m.
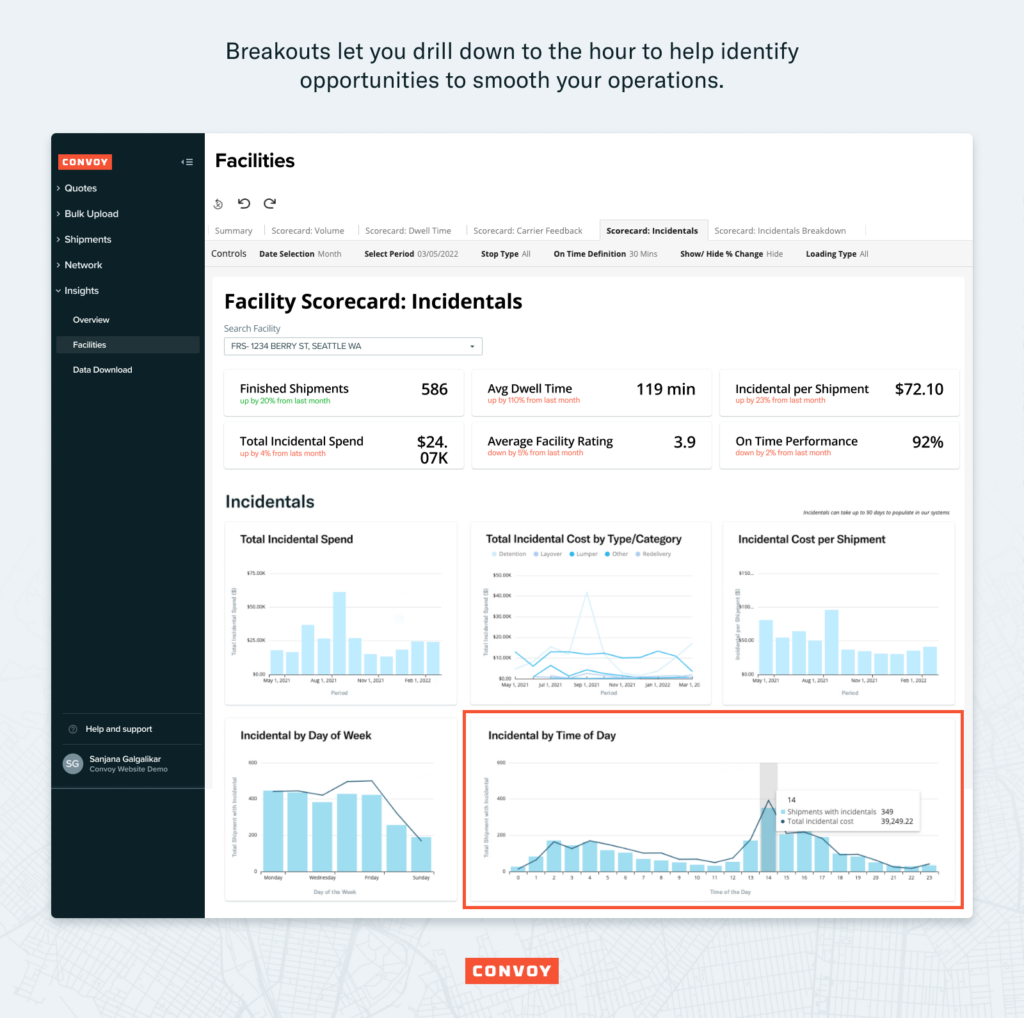
The insight: Convoy recommended the shipper shift some of their morning picks and drops to the afternoon and evening, which was projected to save up to $150,000 per year.
TIP: The most commonly used words in one- and two-star reviews tend to be “wait,” “time,” “hours,” “slow,” and “long.” A suggestion from our Annual Freight Insights Report: Build processes and make improvements that get carriers in and out. Some customers put funds aside for extra dock space. Others, like in the case above, optimized appointment times for their busier days. Others provided more communication and extra signage so carriers know where they should wait, park, and drop trailers.
3. How much more efficient are my drop shipments compared to my live shipments? What would the budget impact be if I shifted more loads to drop?
The problem: This shipper wanted to convert more live loads to drop-and-hook but needed to better understand their live versus drop performance before making the switch. They knew drop as being the most efficient way to ship but couldn’t quantify the difference — Convoy’s insights dashboard could.
The process: The shipper simply toggled between drop and live loads to discover that, although both live and drop shipments were performing better than the industry average, their drop incidental frequencies were half of live’s, and the average incidental per load shipped was 34% less for drop.
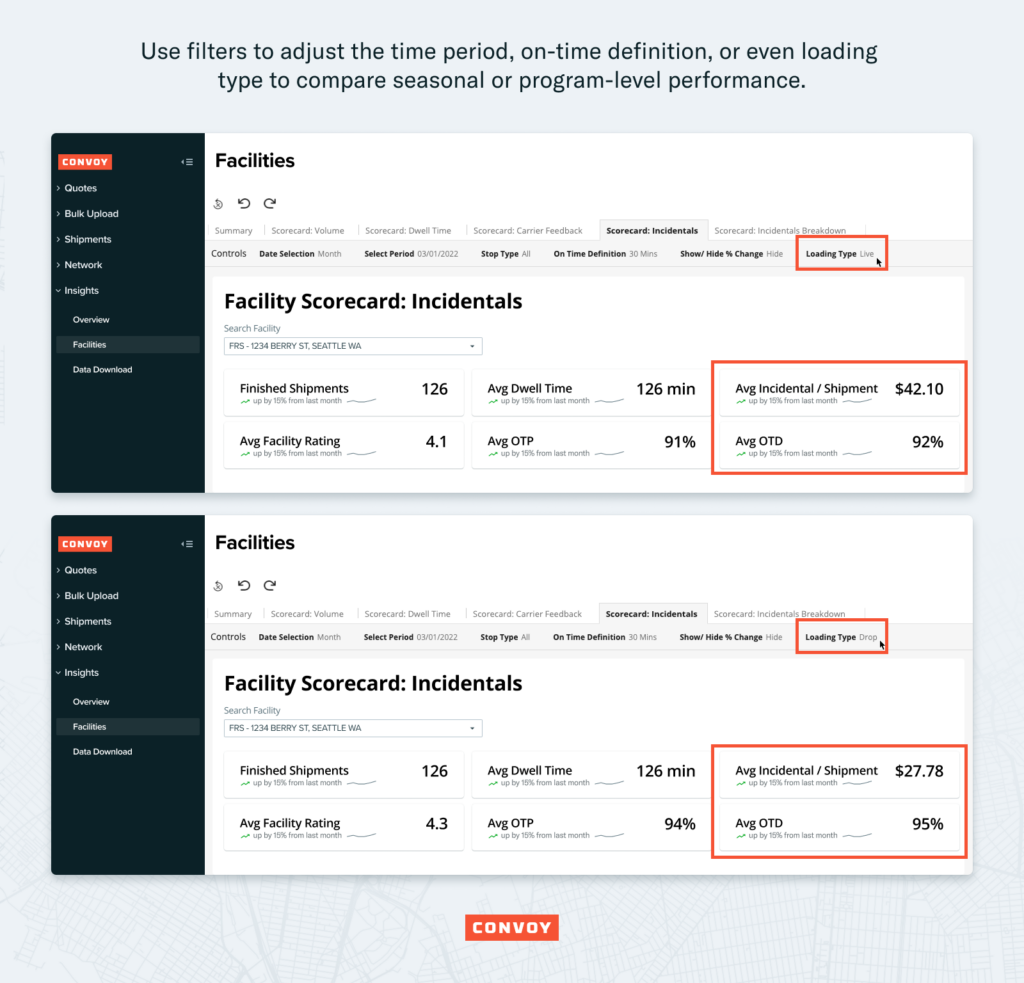
The insight: By increasing the shipper’s load allocation to flexible drop, which provides nationwide drop capacity across primary, backup, and spot, from 6% to 25%, the shipper’s estimated cost savings totaled nearly $86,000.
TIP: Another benefit of converting more live loads to drop loads — drivers prefer them. According to our analysis of carrier reviews for our Annual Freight Insights Report, “easy” was the 7th most common word in facility reviews for drop loads in 2021 but ranked 64th for live loads in 2021. Also, drop loads received more five-star reviews than live loads did.
4. Why do I have excessive dwell times at this particular facility?
The problem: For this shipper, facility insights helped expose excessively long dwell times for both pickup and drop-off, along with the resulting detention costs.
The process: Convoy’s analytics team compared the driver’s actual transit time to the facility’s appointment times, with a stunning realization. Drivers were arriving so early for their appointment times that they were waiting for hours. For example, a driver picked up a load at 9 a.m. and arrived at the facility for delivery at 12:30 p.m. — but their set appointment time wasn’t until 6 p.m. The driver held onto this trailer for close to six hours longer than they needed to.
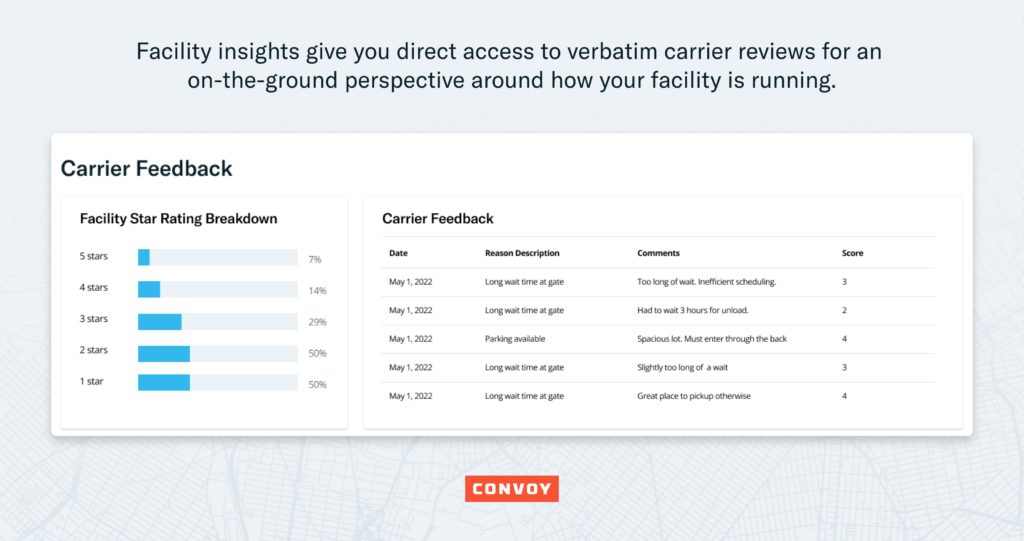
The insight: The shipper’s 3PL managed planning and transit time planning — and the shipper didn’t know about these transit inefficiencies (and their resulting operational and cost impacts). Convoy provided lane-level optimized transit recommendations that led to the shipper expanding their facility hours, implementing our recommended transit time (that their 3PL now executes), which reduced excess transit by 57.3% and pickup dwell time by 57.1%.
TIP: Carriers can haul up to 11 hours a day, as permitted by hours-of-service regulation, but Dr. David Correll, a research scientist and lecturer at the MIT Center for Transportation and Logistics, estimates that long-haul truck drivers spend, on average, 6.5 hours per day working. “This implies that 40% of America’s truck driving capacity is left on the table every day,” he said in his testimony for the House Committee on Transportation and Infrastructure. The industry as a whole needs to be better about respecting carriers’ time, and according to our Annual Freight Insights Report, facilities that are successful earn the highest reviews.
Facility insights brought to you by the nation’s most tech-connected carrier network
Our vast network of small carriers and owner-operators totaling more than 400,000 trucks nationwide provide meaningful insights through the Convoy app. We require app usage to haul loads — this is how we provide GPS tracking on 95% of live loads and 100% of drop loads. It’s how we collect robust data around dwell times, detention costs, and more. To date, we’ve captured more than 2.7 million facility reviews in the Convoy app.
As you’ve read, facility insights and carrier reviews help distinguish a well-functioning facility from one that needs improvement.
Shippers use facility insights to improve their own operational performance and the facility experience for carriers. They can better their chances of becoming a shipper of choice and actually improve their access to reliable capacity. When used wisely, facility reviews and ratings can become a competitive advantage.
Shippers aren’t alone in finding this data invaluable; carriers do, too. For Convoy specifically, 84% of carriers often or always look at ratings and reviews before moving forward with a bid on a Convoy load. Positive ratings and reviews can compel drivers new to your facility to give it a try. For you, that means securing new reliable capacity can be the difference between “I hope to continue working with them” and “Never picking a load from here again.”
Tap into facility insights with Convoy
New to Convoy? Get a demo and learn more about shipping with us. Let’s talk.
Already ship with Convoy? Log in to view facility insights or request access to your account today. With every shipment, facility insights are being updated on your insights dashboard.