Could All Freight One Day Be Drop-and-hook?
Industry Insights, Shippers • Published on May 3, 2022
This story originally appeared in Convoy’s “The Future of Freight,” featuring 40 thoughtfully curated pages on supply chain disruption, freight procurement, market volatility, and more.
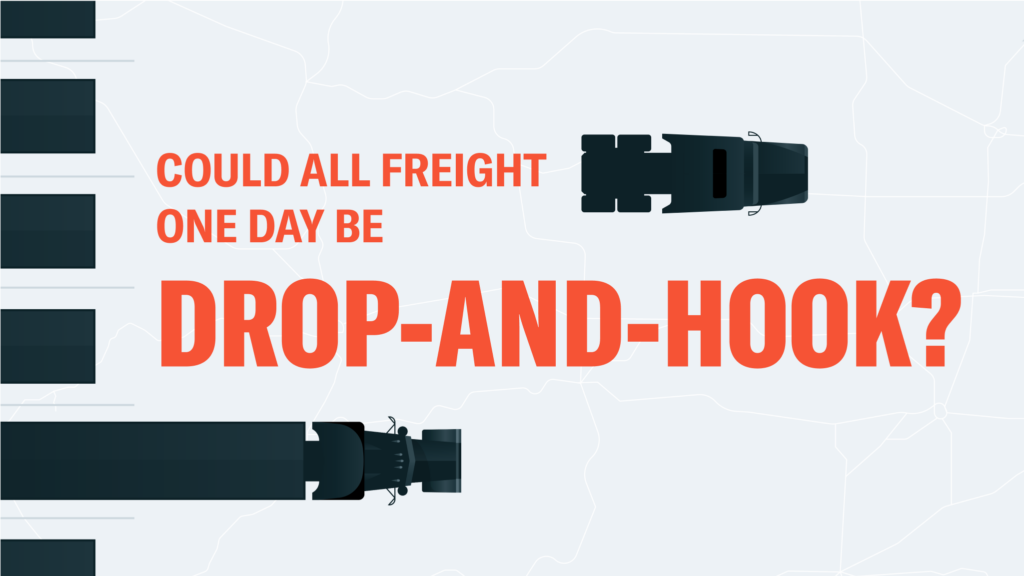
Today, U.S. Fortune 500 shippers move the majority of their freight through preloaded drop trailers. Many of them would move even more of their freight as drop-and-hook loads if they could. Some would forgo live loads altogether.
Transportation teams prefer drop for its flexibility. Facility workers prefer it because they have a much wider time window for loading and unloading trailers. Carriers prefer it because it helps improve their productivity. In running our own nationwide drop-and-hook program since 2019, we’ve seen average carrier load and unload wait times drop from three hours to under 30 minutes, which in turn lowers detention fees for shippers. And the Environmental Protection Agency says drop helps reduce carbon emissions by eliminating hours of tractor idle time.
If drop benefits shippers, facility workers, carriers, and our planet, why aren’t we moving more freight this way? Unfortunately, the operational constraints of traditional drop programs have made this unfeasible. In recent years though, machine learning and automation have enabled an entirely new breed of drop program that operates with a level of flexibility and efficiency never before possible. This opens the question of whether all freight could one day be drop-and-hook. To answer that question, let’s start with what’s traditionally held us back.
Constraints of traditional drop-and-hook
Drop-and-hook freight is substantially more complex than live loads. With drop, you need to match each shipment to an available trailer and a separate tractor. To do that, you need to know where all your trailers and tractors are, and you need to be able to route them to the next pickup as efficiently as possible.
Carriers have traditionally addressed this problem manually — with people on the ground and on the phone chasing assets. The process is time intensive, error prone, and operationally expensive, limiting drop service to large asset-based carriers, running on dense lanes with predictable shipment volume. This is also why drop has been used almost exclusively for contract freight.
But even with the relative predictability of contract freight, shippers incur unexpected costs with traditional drop programs. When tender volume exceeds forecast, transportation teams are forced to supplement with live loads, increasing operational costs and reducing the efficiency of their supply chain. Live loads not only introduce logistical hassles with appointment scheduling and additional labor requirements, but they also increase service quality risk through unfamiliar carriers sourced on the spot market.
Conversely, when tender volume dips below contract expectations, trucks stop moving. Carriers address lower fleet utilization with punitive fees, either charged directly to shippers or indirectly by passing along their higher fixed costs.
When spot market spillover and punitive fees are accounted for, the inefficiency and inflexibility of traditional drop programs cost shippers 9% of annual freight spend on average:
$9.5 million for a shipper that moves 250,000 drop loads a year
$37.4 million for a shipper that moves 1 million drop loads per year
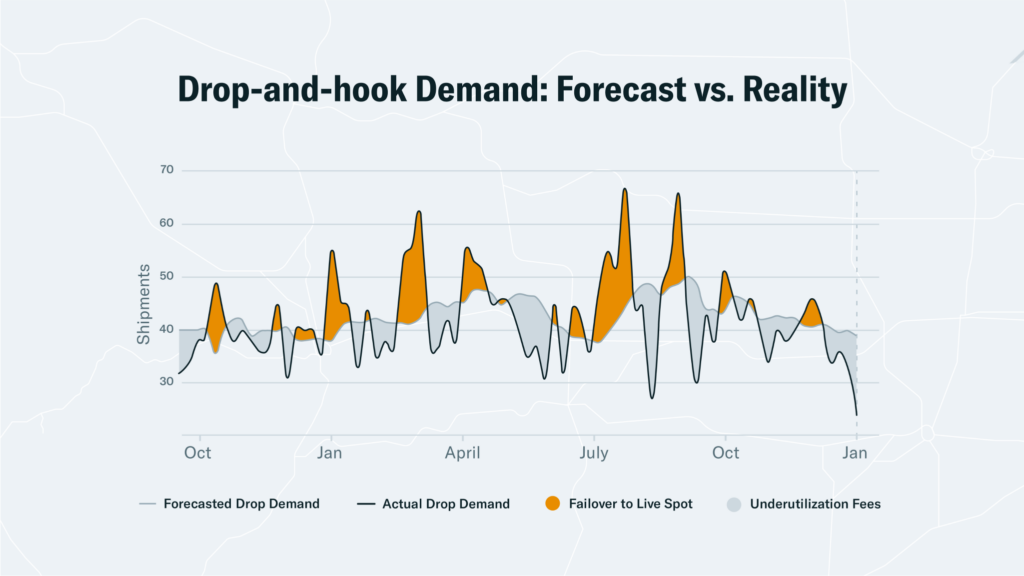
This ongoing cycle of spot market spillover and punitive fees has always been part of traditional drop, creating undue burden and risk for transportation teams and constraining the potential of this otherwise highly efficient form of shipping.
A new breed of drop-and-hook enabled by technology
Building toward a future in which all freight is drop-and-hook requires that we first overcome the limitations described above. In 2019, we took the initial steps by launching a new type of drop program called Convoy Go.
The program flipped traditional drop-and-hook on its head in several ways. First, it opened up high-quality drop shipments to every carrier in our digital freight network. With more than 400,000 trucks, we solved one part of the drop equation — always being able to match a shipment to an available tractor. And through our unique quality and compliance program, we could deliver service quality on par with the industry’s top asset-based carriers.
But what about trailers? Over the last three years, we’ve developed a new kind of drop trailer network, enabled by machine learning and automation technology. It eliminates the inefficiencies of traditional drop-and-hook programs by providing nationwide capacity for primary, backup, and spot loads, and it enables facilities to operate at peak efficiency regardless of fluctuations in demand. Here’s how it works.
Smart trailers
Every trailer in our network is equipped with internet-connected sensors that provide insights into the asset’s location, condition, and status. This eliminates the need for a large team of people to manage trailers on the ground.
The trailers report their location using GPS and geofencing, so we can track 100% of our drop loads en route. We not only see where the trailer is but also how fast it’s moving and, with the help of machine learning models, when it’s expected to arrive. Additional sensors and proprietary software tell us whether the trailer’s loaded, what it was carrying previously, and what it’s slated to carry next. We can even determine whether a trailer has been stolen, an increasingly important capability as cargo theft has accelerated in recent years. With the increased visibility offered by smart trailers, you never have to wonder about the location and status of your shipments.
These sensors also give us a detailed view into your facility yards. We can see how many trailers are parked in the primary and overflow lots, each trailer’s parking spot, whether the trailers are empty, and which are ready to be unloaded or dispatched. While asset carriers rely on dedicated equipment teams to manually check trailer status, Convoy Go provides this information automatically and without manual inaccuracies or the overhead costs of a dedicated team.
Trailer rebalancing
Supply and demand between facilities and cities is rarely equal. You might have a lot of freight going from Los Angeles to Phoenix, but few loads headed in the reverse direction. This leads to trailers piling up in cities with high demand. Traditional drop programs address this by deploying a surplus of trailers and constraining each trailer to a closed loop between two facilities. This is an inefficient use of trailer capacity and results in higher operating costs.
We’ve taken a different approach using machine learning technology. Each day, our machine learning models route trailers to where they’re needed in advance of the next pickup. As part of this, Convoy Go trailers are shared across our customers — a universal trailer pool that flexes with shippers’ fluctuating demand. Doing this at a nationwide scale involves analyzing billions of permutations to identify the most efficient route for every tractor and trailer. We account for loads that have already been booked, and we can reliably predict our customers’ future trailer demand weeks in advance.
The result is that we can find a trailer for our customers’ drop shipments 99.9% of the time. And in almost every instance, we deliver the trailer more than 24 hours in advance of preload.
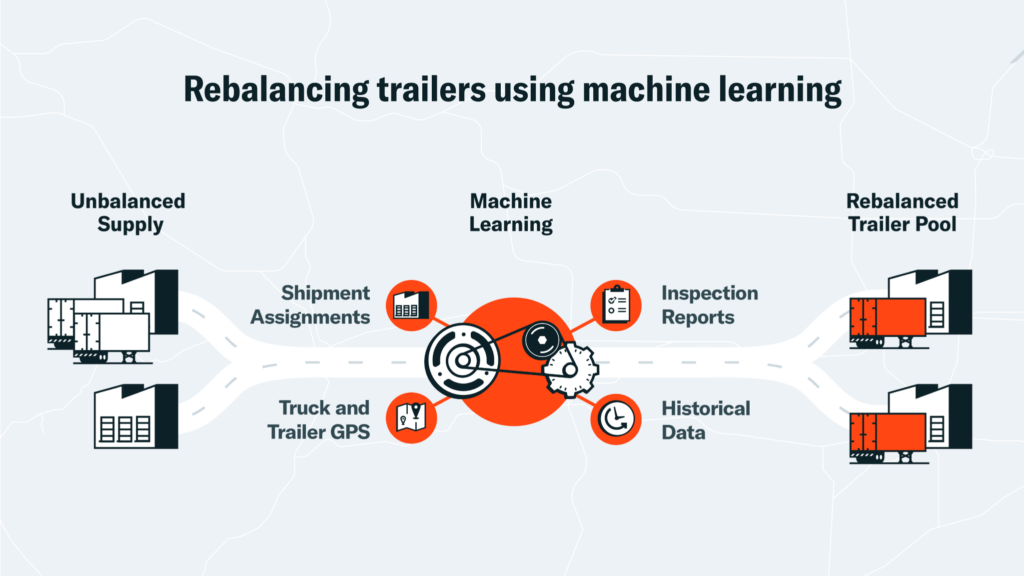
Automated Reloads
Automated Reloads enable drivers in our digital freight network to automatically match their headhaul with a backhaul, earning more money on each run while achieving better truck utilization. For shippers, these reloads reduce carrier cancellations by roughly 10%, and they significantly reduce carbon emissions from empty miles. We’ve been offering this capability on live loads since 2019, and we recently introduced automated reloads for drop shipments as well.
In the example here, the carrier drives approximately 55 miles empty — 45 miles between Portland, OR, and Salem, OR, to pick up the backhaul, and an additional 10 miles between Bellevue, WA, and Seattle after dropping the backhaul. This is compared to driving approximately 175 empty miles from Portland to Seattle had we not found a backhaul shipment.
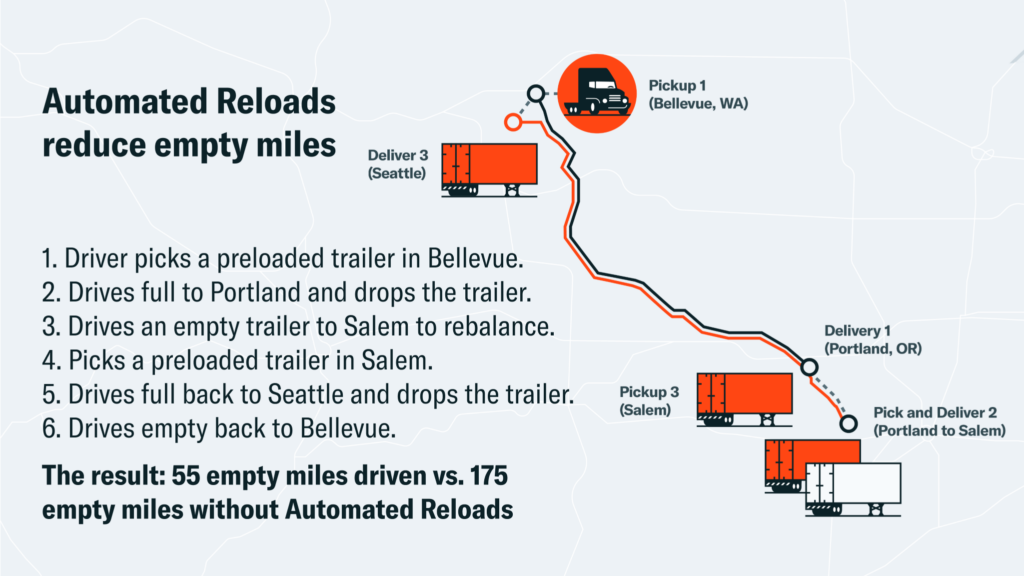
By bundling multiple shipments together, Convoy helps carriers reduce their carbon emissions from empty miles by 45%. As of April 2022, Convoy has saved more than 8 million pounds of carbon emissions from entering the atmosphere.
So could all freight one day be drop-and-hook?
I believe we’re on a path to enabling the vast majority of freight to move in drop trailers. We’ve laid the foundation with a more efficient, flexible, and sustainable drop program in Convoy Go.
The next step is to further unlock trailer capacity. This isn’t simply a function of accelerating new trailer production, although trailer manufacturing will need to recover to some degree, potentially aided by new, more accessible construction materials. The more immediate opportunity, though, is to unlock latent capacity in idle assets — estimates are that 20% of trailer fleets sit unused on any given day.
This will require industry collaboration across shippers, carriers, digital freight networks, trailer manufacturers, and drop yard providers to build a truly universal trailer pool across the 4.8 million trailers currently in service. We’re already pursuing this vision, and we’re looking for innovative, forward-leaning partners to join us.