Improving Supply Chain Resilience with Shipper Insights
Data Science, Industry Insights, Shippers • Published on May 28, 2020
Every day when your loads are picked up and dropped off at facilities around the country, how do you know which of your warehouses and distribution centers are performing well and which aren’t? For example, if one of your warehouses started experiencing higher detention rates, how quickly would you find out, and how easily could you diagnose the problem?
For many shippers, business insights like these aren’t readily accessible, creating a blindspot in their supply chain operations. For companies who ship with Convoy, this critical information is always available through the use of our network insights products and services.
Turning Data into Business Insights
Network insights track the lifecycle of your freight – the journey a load takes from initial tender through pickup and all the way to delivery and carrier payout. Along the way, our digital freight network collects more than 1,000 data points about your facilities, wait times, incidentals, shipment performance, and more. We then use machine learning to analyze the data, and with the help of our data scientists and supply chain strategists, we surface business insights to our customers’ logistics teams through reports, online tools, and custom engagements, offering a level of supply chain visibility never before possible.
This type of information can be particularly valuable when navigating supply chain disruptions and volatile market conditions like those created by the COVID-19 crisis. In a matter of weeks, our industry saw tightening and softening market conditions that normally play out over the course of many months. And during this time, Convoy had the privilege of partnering with our customers in every industry, helping them understand how their supply chains were responding to the demand shocks, and recommending changes to make their systems more resilient.
Responding to a Demand Surge
As the COVID situation escalated in early March, one of our shipping partners experienced a massive flood of customer orders, causing weekly tender volumes to double. Fortunately, Convoy’s digital freight network was built for such situations. Our tens of thousands of carriers were able to swarm to the areas of greatest need, absorbing much of this shipper’s surge and accepting 30% more tenders than in pre-surge periods without compromising on on-time delivery (OTD).
More importantly, we were able to use data collected from thousands of shipments to show how the shipper’s supply chain was overwhelmed by the sudden surge in volume, the costly downstream operational impact, and how operational bottlenecks could be avoided in the future.
When the deluge of customer orders came in, our shipper’s tendering system automatically created shipment requests to fulfill each order. Unfortunately, the number of shipments created far exceeded their facilities’ loading capacity for the period, causing the percentage of shipments with blocked appointment requests to double. This created a domino effect. Loading facilities got backed up as they scrambled to work carriers in, extending wait times by an average of 90 minutes. Pushed pickup appointments and long loading delays made “requested delivery date” (RDD) failures twice as likely, and cascading operational issues caused a 40% increase in incidental cost per shipment.
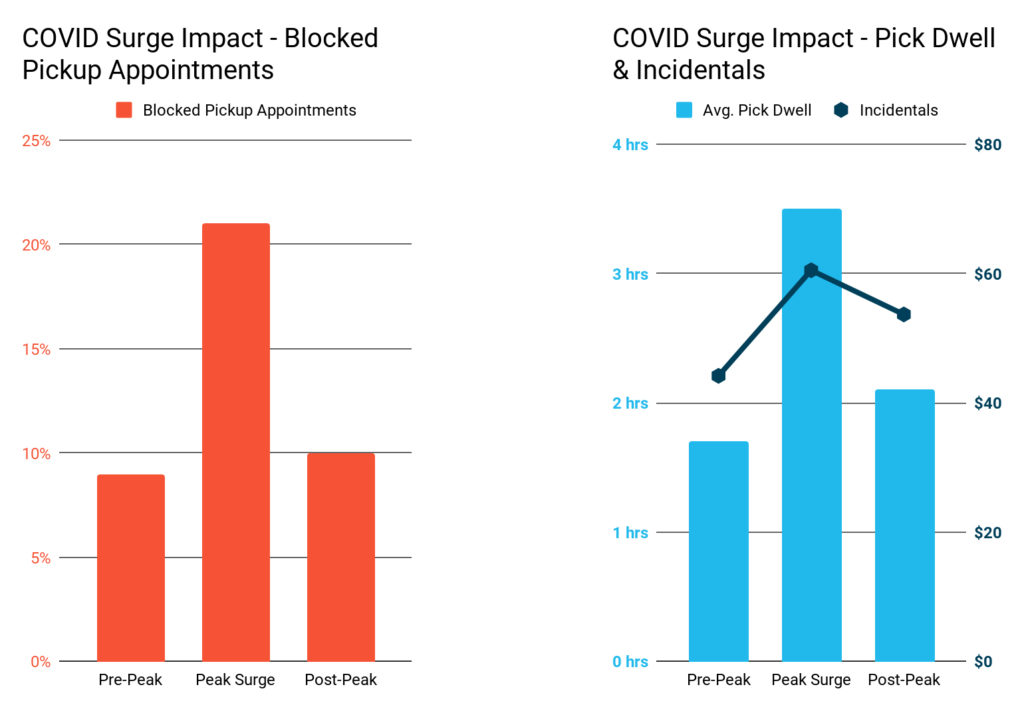
Once we’d identified the root cause of the problem, we were able to recommend changes that would improve the durability of the shipper’s tendering system. Specifically, we recommended building failsafes into the tendering system that would prevent the automatic creation of shipment tenders when order volume exceeds a given threshold. This would give the shipper greater control over their network during volatile periods and allow them to be more strategic in considering the tradeoffs between volume and operational efficiency.
A New Kind of Freight Partnership
Each of our customers has a supply chain and set of operational processes that are unique to them. And the logistics professionals we’re lucky enough to work with each day know the intricacies of their transportation systems in a way we can never hope to.
However, through the use of thousands of data points collected on every shipment, machine learning, and dedicated Convoy team members, we’re able to partner with shippers to uncover hidden inefficiencies in their supply chains and help them identify ways to improve their operations, lower their shipping costs, and improve the resilience of their systems. It’s one of the things that differentiates a digital freight network from traditional brokers and asset-based carriers, and it’s one of the most rewarding parts of what we do at Convoy.
With market volatility increasingly looking like the new normal, a digital freight network can help you optimize your operations and respond more quickly to demand shocks. As Gartner analyst Bart De Muynck recently wrote, “Digital freight networks can help companies that are looking for real-time available capacity or looking to reduce transportation costs during the current crisis, as well as during future challenging times.”
If you’re looking for new ways to build resilience into your supply chain, we’d love to help. Just fill out the form on this page and a member of our team will reach out to learn more about your specific needs. Or if you’re interested in learning more about the types of supply chain insights that Convoy could provide, check out our latest white paper, Supply Chain Visibility and the Digital Freight Network.